Kurita America’s development and application of antioxidant chemistries improve the quality of ethanol plant coproducts. The years of international experience coupled with local legacy to create OxiOUT, which is a stable solution of sodium metabisulfite and other proprietary antioxidants. After thorough review of the coproducts and what the quality issues are, our innovative chemistry leads into the application and the provided value.
At the base of ethanol is corn, and at the base of corn is approximately 61 percent starch, 3.8 percent oil, eight (8) percent protein, 11.2 percent fiber, and 15 percent moisture. During production, starch is converted to ethanol, and the other constituents of the corn kernel become coproducts. Each bushel of corn produces 2.7 to 2.8 gallons of ethanol, approximately 18 pounds of distillers grains plus solubles and 18 pounds of carbon dioxide. Recent figures show that United States fuel ethanol was up approximately one (1) percent for the week ending July 2nd, 2021, which is an additional 9,000 barrels per day when compared to the same time last year, now averaging 1.067 million barrels per day.
For those 18 pounds, distillers grains are the primary coproduct that is widely used as feed for livestock. It is marketed as dry distillers grains with solubles (DDGS), modified distillers grains with solubles (MDGS), or wet distillers grains with solubles (WDGS). According to data from North Dakota State University, approximately 42 percent of distillers grains is fed to dairy cattle, 42 percent to beef cattle, 11 percent to swine, and five (5) percent to poultry. Annually, North Dakota produces more than 1.3 million tons of distillers’ grains and associated coproducts.
There is an oxidation reaction that alters the characteristics of wet distillers grains, making the feed less palatable for livestock and more prone to mold and spoilage. Corn oil suffers too as the oxidized fats can foul equipment and reduce efficiency in the conversion to biodiesel. Other oilseed products oxidize, creating issues of rancidity and cloudiness in the oil and reduced value of the feed.
These issues include mycotoxins, also known as mold poisons. Molds themselves can adversely affect the health and productivity of cattle. Ingestion of moldy feed or hay can potentially cause mycotic (fungal) abortion, respiratory effects, decreased feed consumption and rate of gain, and digestive problems. Tolerance levels are not well established for ruminants because they have microbes in their rumen that act to naturally detoxify mycotoxins. This ability makes ruminants relatively resistant to these toxins and is probably why few problems from mycotoxins are recognized. However, high producing animals, such as dairy cattle, have an increased rumen passage rate; this faster processing of contaminated feed may overwhelm the rumen microflora, so that they will not be able to denature all the toxins. Young calves do not have fully developed rumens and are therefore also more susceptible to mycotoxins. Even though mold is seen, mycotoxins may not be present. Molds only produce mycotoxins under specific conditions of temperature and humidity.
At certain times of the year, particularly in the summer months, the price for coproducts is attractive enough to warrant stockpiling and storage. WDGS and MDGS can be stored in an oxygen-limiting environment, such as plastic silage bags, as a means of prolonging storage by limiting oxygen penetration. However, filling the bags can be difficult; if bags are packed too tightly, then they can split as the WDGS or MDGS settle. Care should be taken to not overpack the bags too tightly. Holes should be patched or covered promptly to prevent spoilage. Wet distillers grains plus solubles can also be stored in bunker-type silos and covered with plastic, but some spoilage should be expected with this storage method. Much of this goes back to chemistries of the antioxidants.
The basic definition of antioxidants are substances that can prevent or slow the damage to cells caused by free radicals. Oxygen is the most well-known free radical. Antioxidants help neutralize free radicals in our bodies and boost overall health. One well-known example is beta carotene, which converts to vitamin A (retinol) to support eye health. Beta carotene may also help improve long-term memory and cognitive function. Another antioxidant would be inorganic salts, such as sulfite, which have been used as food additives due to their preservative properties. In fact, they have been used as a food additive since 1664 and have been approved for use in the United States for more than a century.
In a real-life example, Kurita America was working with a plant that was seeing spoilage of a wet cake once it was reaching the end customer. The process began to develop a new chemistry option to combat the negative effects of oxygen on a wet cake. After initial product development, Kurita America began small-scale bench testing and then moved the application to the full-scale process while being conscience of the economics and regulatory requirements.
For product development, Kurita America started with the challenge of improving the shelf life of a wet cake. To counter the spoilage issue, a material was needed with antioxidant properties. Kurita America developed the product OxiOUT 1000— or just OxiOUT— to follow regulatory guidelines and proper planning for production and distribution. Realizing that this product could help many customers, Kurita America went through development.
The first step following development was small-scale testing to determine the effectiveness of the new chemistry. The small samples of the wet cake had one portion treated and one portion untreated. The development of key indicators of oxidative degradation is tracked over time under a range of real-world conditions. After seven days, the untreated material started to develop mold growth; the treated sample had no noticeable growth present. Within 30 days, the untreated sample had exploded with mold growth, and the treated sample still had no noticeable growth. This validated the treatment with the antioxidant chemistry. Similar testing was completed at multiple facilities with the same results.
Regulatory requirements needed to be completed prior to full-scale evaluations. Since these chemistries must be fully compliant with the requirements of the Food Safety Modernization Act (FSMA), a full discussion of their properties and action documents their importance to an ethanol producer. OxiOUT 1000 contains no carcinogens or deleterious compound or raw material more than the amounts listed in Food and Drug Administration (FDA) regulations spelled out in 21 CFR 170-189. This product would be appropriate for use in any food plant subject to the FDA regulations and for any facility subject to inspection by the United States Department of Agriculture (USDA) Food Safety and Inspection Service (FSIS), including meat, poultry, and pasteurized eggs. All ingredients used in this product are those found in 21 CFR 184 Direct Food Substances affirmed as Generally Recognized as Safe (GRAS) and/or 21 CFR 582 Substances Generally Recognized as Safe (in animal feed). It was certified for each state that it is used or consumed and importantly GRAS certified and FSMA certified. With this, Kurita America moved onto a plant-sized evaluation of the antioxidant.
In a full-scale application, the chemistry was available in a 275-gallon tote and was fed with a small chemical pump. The pump fed to a pigtail spray nozzle that applied the material to the wet cake as it passed along the conveyor to the wet cake pad. A simple feed setup could be turned on and off as needed, depending on the wet cake production. Since the end customer was able to increase the longevity of the feed, the plant was able to increase the sale price for their wet cake by $5 per ton. When we compared the application cost to the increased revenue of the coproduct, there was an average increase in annual revenue of $343,000. From 2017 to 2020, the increase was $1.4 million in total. While this is a great increase for this plant, it was largely due to their location and vicinity to feed customers. Some locations will not have enough time for spoilage to set in and will not see an added benefit with the antioxidant treatment.
The benefits of the OxiOUT program with this unique antioxidant treatment from Kurita America provided an increased quality product that satisfies the producer and the end user, a very simple set up that added significant value, and smooth transition for the plant at a low cost. With this treatment method, Kurita America has successfully extended the useful coproduct shelf life and maximized the value to their overall operation. Other applications are being pursued in the same fashion with the same end goal of increasing plant coproduct profitability. Each facility wants to ensure co-product quality and value. Some are diversifying beyond ethanol and adding streams for the productions of United States Pharmacopeia (USP) grade alcohol for hand sanitizers or other industrial alcohol applications. Overall optimization of the coproducts produced at each facility is essential for continued economical plant operations.
Kurita America’s coproduct optimization with OxiOUT 1000 offers longer shelf life for a wet cake while the chemistry addresses quality concerns and provides added value as shown by the development and full-scale applications. All of this enables us to deliver optimal results and overall lower cost of ownership for our customers while conserving natural resources for a more sustainable world.
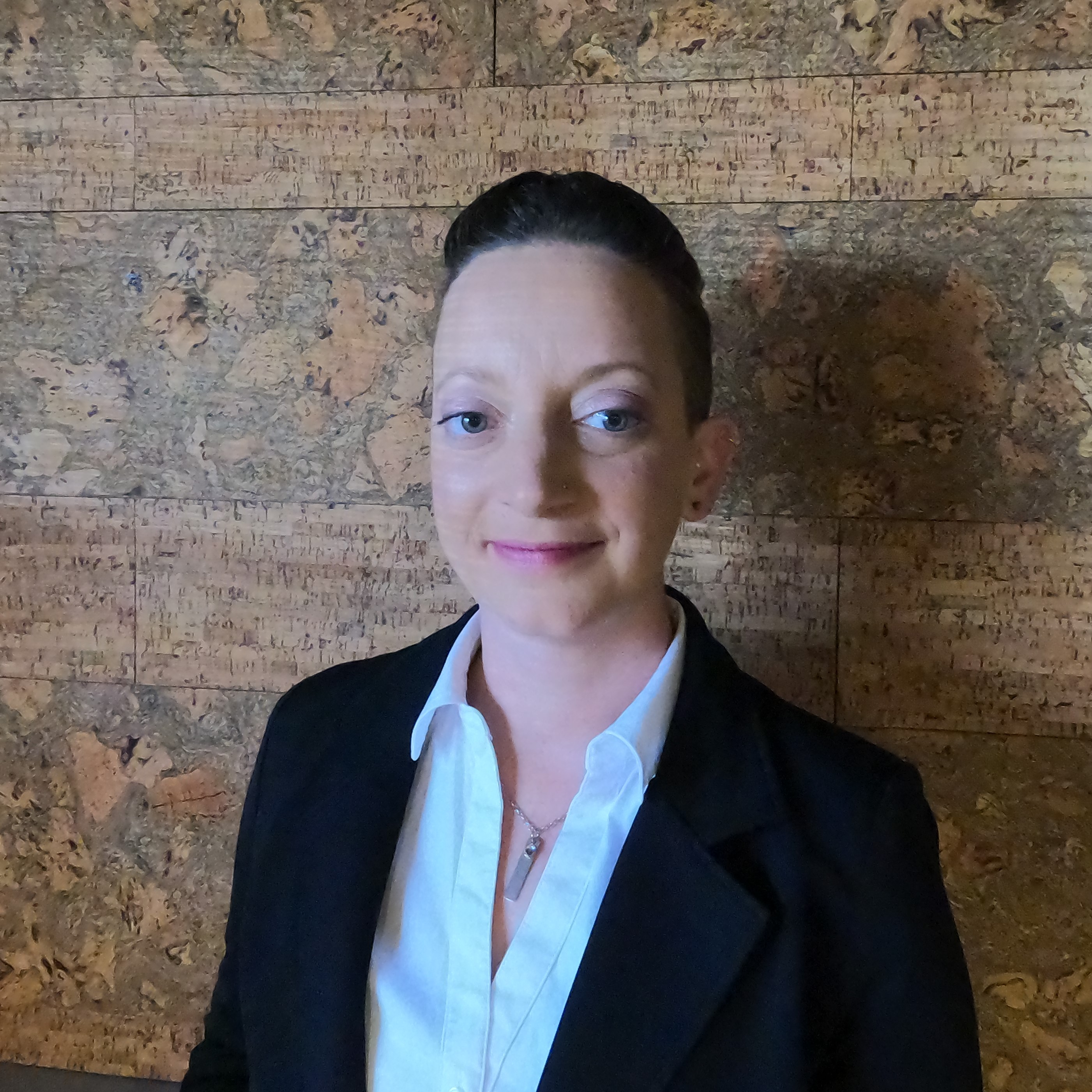