After an ethanol plant initiated some significant process changes, they encountered a final product sulfate issue that they had not faced before. Although the process changes provided excellent yields and the related economics were sound – meeting the final product quality specifications for sulfate became a problem. Blending provided a degree of relief, but created logistical challenges. The customer looked to the Kurita America Process Technologies (PT) Team for a solution.
EPT offered support based upon their experience in developing and implementing sulfur control systems. A review of the plant’s operations led to the recommendation of deploying an integrated approach – combining chemical, mechanical and operational components, including the application of a Ethanol Final Filter (EFF) system. Installed in mid-July 2014, this unique and proprietary system has successfully treated 200 proof ethanol en-route to storage, and has resolved the plant’s sulfate issue.
Since 2007, the PT team has worked with both vacuum and pressure distillation plant designs to manage acidity, pHe and sulfate quality parameters. In 2010, ethanol producers approached Kurita America for a targeted specific solution to high sulfate content product in tanks and railcars.
EPT began by constructing and installing a bench-top simulator at an operating fuel ethanol plant and evaluated many systems and designs using the operating plant’s product. The team then compared analytical techniques for feed-forward to the appropriate American Society for Testing and Materials (ASTM) subcommittee. On-site analyses were performed to evaluate operational parameters of flow, treated volume and regeneration design under a broad inlet concentration range.
Based on the laboratory results, Kurita America constructed and deployed a prototype EFF unit, built for mobile application. The prototype unit trial took place in October 2012 at a central United States fuel ethanol plant. While at this plant, the unit returned severely out-of-spec contaminated railcars of denatured and inhibited fuel ethanol, back to spec.
The plant was the first home to a full sized commercialized EFF system. The unit quickly demonstrated its ability to dramatically reduce existent sulfate and potential sulfate, even during inlet excursions to greater than 30 parts per million (ppm). Flow rates up to 189 gallons per minute have been demonstrated. In the ensuing 22 months of operation, over 100 million gallons of ethanol has been treated at this location alone. EFF sulfate control has been continuous with minimal interruption since start-up. Treated product has consistently met the 4 ppm sulfate standard throughout.
After the success of the mobile prototype, PT moved the system to permanent service at another central United States fuel ethanol plant – where it provided long-term reductions in both existent and potential sulfate with no unintended consequences.
Building upon the positive results of the prototype unit, Kurita America commercialized and introduced the Ethanol Final Filter to the ethanol market in 2014. This bolton, mechanical/chemical system is unique to the industry due to its ability to improve final fuel quality through the removal of both existent and potential sulfate. In addition to sulfate removal, the EFF addresses issues of color, turbidity, acidity, pHe, chloride and iron.
Since its commercialization in 2014 – additional Ethanol Producers have incorporated the EFF into their quality assurance programs as a means of ensuring steady state compliance with sulfate-specific specifications in their final product.
Ethanol Final Filter Commercialized; Problems Solved at Fuel Ethanol Plant
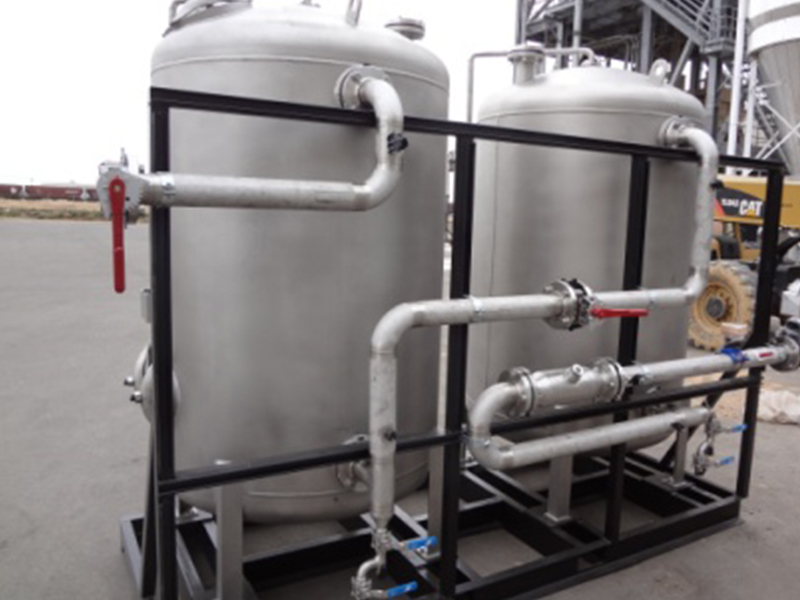