Corrosion in industrial and commercial water treatment continues to be a major concern as companies strive to reduce costs while maintaining their assets. The need to protect heat exchange equipment and associated piping is vital in minimizing operational costs and preventing downtime. Traditionally, copper and carbon steel have been the metallurgies of choice for comfort heating and cooling heat exchange equipment. However, aluminum is becoming an increasingly attractive option for heat transfer as it has a high thermal conductivity relative to its initial capital cost1. While this is an alluring option, it adds challenges to current water treatment programs.
Aluminum is a much more anodic metal than iron and copper, increasing its potential for galvanic corrosion which can lead to devastating effects. Aluminum is also an amphoteric metal with its protective oxide film being soluble at both low and high pH. Because of this, aluminum boiler manufacturers often recommend a lower pH range for optimal protection (8-8.5). This places the water treatment professional in a difficult position, as this raises the corrosion potential for carbon steel, which prefers a higher pH (>9.0). For systems containing aluminum heat exchangers, the need to provide corrosion inhibition for all metal surfaces has never been greater.
Filming Amines
Filming amines have been around for decades, and in the water treatment space, are most often used in steam boiler applications. While their use as primary corrosion inhibitors have been limited, they are receiving increasing attention in heating and cooling water applications. Film Forming Amines (FFA’s) are being considered for application in both closed and open cooling water systems, as they are biodegradable, and leave no hazardous by-products. FFA’s have a strong affinity for metal surfaces, likely due to the partial positive charge on the nitrogen atom as the amine comes into contact with metal surfaces. This attraction is exacerbated by the hydrophobic tail, further pushing the amine away from water and toward the metal surface, leaving a tightly packed film with hydrophobic tails protruding outward2. Polyamines, which inhibit corrosion in a similar mechanism to monoamines (Figure 1) are often preferred as they can form a more resilient film. Film formation is a dynamic process where constant attachment/detachment is taking place, the additional secondary amine provides an extra binding site between the FFA and the metal surface.The de-wetting of the metal surface (Figure 2) inhibits corrosion by preventing dissolved gases and water from reaching the metal surface. This unique inhibition mechanism is becoming increasingly appealing to water treaters as this technology allows the film to be maintained by feeding product at a low residual level. Having a resistant film for corrosion inhibition provides additional leeway for system upsets, or times of suboptimal feeding; unlike neutralizing amines which are quickly consumed by carbonic acid. The application of filming amines can be tightly controlled when combined with a fluorescent tracer and commercially available filming amine residual tests. It should be pointed out that the high affinity between filming amines and the metal surface means they are able to penetrate existing deposits and corrosion debris quite well. When applying FFA’s for the first time to systems previously fouled with deposits or corrosion by-products, it is suggested to start with a very low dose and gradually increase the levels. This will help to avoid excessive sloughing off which can cause blockages in small diameter passages or in low flow areas.
Traditional Treatments
Nitrite is one of the most commonly used corrosion inhibitors for closed loop systems, as it’s relatively inexpensive and the chemistry is well understood. Nitrite acts as a mild steel corrosion inhibitor by oxidizing the metal surface to form a protective Fe2O3 film. However, nitrite provides no aluminum protection, and can even be aggressive to aluminum surfaces3. In lower temperature (<140°F) hot water systems, nitrite can become susceptible to microbiological growth from both nitrifying and denitrifying bacteria. Nitrite reacts with oxidizing microbicides to form nitrate, and therefore should not be used together. Other disadvantages include its relatively high toxicity, and strict discharge regulations. Molybdate, which can be a bit more costly, is known to provide corrosion protection for both aluminum and mild steel. Unlike nitrite, it’s not vulnerable to microbiological degradation, but does require the presence of dissolved oxygen to form its protective oxide layer on mild steel. Protection of aluminum with molybdate is most effective in a relatively tight pH range (7.8-8.3). Above this range, aluminum will become more susceptible to corrosion, and if below, mild steel corrosion rates may not be acceptable.
Silicates are very cost efficient corrosion inhibitors and are known to exhibit some corrosion protection for all metals. Similar to molybdate, they are not degraded by microorganisms, and operate in a similar pH range. While silicates can be used for many applications, they are most commonly used as an adjunct to enhance other treatment programs.
Experimental Methods
Hot Closed LoopCoupon testing was performed using a 10 gal, 3000 Watt hot water heater, circulation pump, and CPVC corrosion coupon rack (Figure 3). Each test run lasted 14 days and was maintained at 160°F. The circulation pump was able to provide a flow velocity of 1.0 ft/sec through the coupon rack. While this is lower than the recommended 3-5 ft/s, relative data is still recognized to be valuable and quantifiable. Soft water was used to triple rinse the system prior to each run. The rinse water was circulated for 10 minutes at room temperature. Makeup water for each test was prepared separately and was pumped into the water heater. Makeup water for all trials remained the same (Table 1).
Cold Loop Testing
Filming amine technology was also tested for efficacy in open cooling systems using a small circulating water loop with LPR corrosion probes (Figure 4 and Figure 5). Makeup water for each trial was prepared directly in the bulk tank. Water analysis shown below (Table 2). The entire system was triple rinsed with DI water between each run.
56.78L of DI water was added to the feed tank prior to salt additions. Salts were left to mix for 30 minutes in bypass loop before treatment addition. After treatment addition, the bypass loop was closed allowing flow though coupon rack and probes. Corrosion data was obtained from Cosasco Corrators® located in a coupon rack with a flow rate of 4 ft/s.
Results and Discussion
Hot Closed LoopA control trial was run to obtain baseline corrosion data for all metals. A pH of 8.2 was chosen as it is within the upper limit proposed by some aluminum heat exchanger manufacturers, and is in the limits recommended by AWT for mild steel protection in multi-metal systems. Multiple trials were then performed with a variety of “traditional” hot closed loop treatments (Table 3). A nitrite/silicate blend was initially evaluated as a multi-metal corrosion inhibitor (trial 2) at a typical operational pH (9.6) for mild steel protection. While mild steel and copper were well protected, nitrite failed to protect aluminum. Results showed aluminum protection is not viable with a nitrite program at it’s native pH, and may even have had an antagonistic effect on the aluminum due to the high corrosion rate. Another traditional chemistry, molybdate/silicate, was tested (trials 3 and 4). Test runs were performed at both the naturally derived pH (9.6), as well as a pH adjusted (8.2) run with citric acid. Results, as expected, clearly indicate this combination to be an effective corrosion inhibitor for all metals tested at the lower pH (8.2). While, a combination of molybdate and silicate is known to provide aluminum protection, its high performance at pH of 9.6 was unexpected.
In addition to traditional treatments, greener chemistries were also evaluated. Trials 5 and 6 included a commercially available tannin product. Both tannin trials with and without an azole adjunct did not perform well relative to the control under the conditions tested. Interestingly, even at a pH of 9.0, mild steel corrosion was higher than the control with a pH of 8.2. The high aluminum corrosion rates can likely be attributed to higher pH and an increase in iron in the bulk water.
A commercially available filming amine (trial 7 and 8) product was tested and compared to a newly developed FFA formulation (trial 9 and 10). Both products were initially tested at the upper recommended dosage of 5000 ppm as product. At this level there was no indication of copper or aluminum corrosion in the 14-day trial with either formulation. Mild steel rates were well within the accepted limits, all while operating at lower than desirable pH for mild steel protection. The results of trial 9 showed a mild steel corrosion rate of 0.03 MPY at a pH of 7.8, within manufacturers recommended limits. Both filming amine blends were tested at the lower end of the usage range (1000 ppm). The commercially available filming amine showed some improvement on mild steel and copper compared to the control, but didn’t provide aluminum protection at this use level. The results (Trial 10) for the newly developed FFA at the lower dose were comparable to the results at the 5000 ppm dose. Only a slight increase in mild steel corrosion is observed, but still within the acceptable limits.
Aluminum corrosion coupons for select trials are shown in Table 4. Trial 3, the molybdate/silicate blend, serves as a benchmark of traditional treatments. Coupons from this trial clearly shows a clean aluminum surface in comparison to the control and tannin trials. The improved performance of the filming inhibitor (trial 10) is an indication of how viable this technology is.
Cold Loop
Most available filming amine data comes from hot water or steam related systems. It has been previously shown FFA adsorption increases at higher temperatures4. As filming amine technology is being considered for other applications, a study was conducted to determine viability as a corrosion inhibitor in an open cooling circuit. Figure 6 shows the mild steel corrosion rates varying doses of filming inhibitor, dose levels are as active filming amine.
The relatively aggressive nature of the water used in the test (see Table 2) quickly corroded the LPR electrodes in the control run, reaching 20 MPY in under four hours. A dose of 5 ppm FFA significantly reduced initial corrosion rates as compared to the control. However, the trend still indicates an increasing corrosion rate towards the end of the run. The results indicate the FFA provided some level of protection but the initial dose was not sufficient to adequately film the entire surface. The 10 ppm dose behaved in a similar manner to the 5 ppm dose up to the 4-hour mark. At this point a steady decrease in corrosion is observed, and indicates there was sufficient FFA present to satisfy the surface demand and form a dense, protective film on the LPR electrodes. It should be noted the results of this test only demonstrate the need to satisfy the demand from all the system surfaces in order to achieve adequate corrosion protection. The initial dose and time required to achieve protection will vary, as film formation is heavily dependent on surface area, water volume, and temperature. Systems with previous fouling, deposition, or build-up of corrosion by-products may exhibit significant sloughing and deposit removal. This will also increase the initial demand of the FFA.
Corrosion data was also monitored for several days after the initial 10ppm dose in order to determine the film stability (Figure 7). NaOCl was used to treat the circulating loop and residual Cl2 levels were maintained at 0.2-0.5 mg/L. As expected, the filming amine did not appear vulnerable to oxidation at the levels of chlorine applied. Corrosion rates were maintained ~1.5 mpy for six to seven days with only the initial dose. Several amine residual tests were taken over the 11-day period after the initial 10 ppm dose. A rose bengal test method for aliphatic amines was used measuring absorbance at 560 nm with a Hach DR890 spectrophotometer. Three and a half hours after the application of the initial dose, a sample was tested yielding a residual level of 7.96 mg/L. Another sample was tested at 5.5 hours indicating 5.03 mg/L of FFA remained; nearly a 40% loss.
A correlation can easily be seen in the first few days of testing between residual FFA and corrosion rates. Corrosion rates sharply decline as the film begins to form in the first two days. From two to eight corrosion rates remain relatively steady as residual filming amine slowly decreases to <0.2 mg/L. At day seven a residual of 0.06 mg/L was measured without a noticeable increase in corrosion rate. It wasn’t until the final measurement of 0.03 mg/L was a corresponding increase in corrosion noticeable. Testing indicates that after initial film formation has occurred, residual levels need to only be maintained at near the detection limit to maintain corrosion inhibition.
Summary and Conclusions
Comparative testing of corrosion inhibitors was performed in a circulating hot water pilot system (160°F) containing copper, mild steel, and aluminum. Efficacy of traditional chemistries, as well as filming chemistries was determined by metal loss over a 14-day test period. Results clearly show the filming amines were the most effective corrosion inhibitors for all metals tested at the pH range (8.0-8.5) recommended for protection of aluminum. Results using a nitrite/silicate blend show the difficulty in protecting mild steel and aluminum simultaneously (trial 2). To effectively protect mild steel, a high pH (9.6) was needed. This consequently resulted in a corrosion rate of 378 mpy for aluminum. A cold water circuit was also used to evaluate the film formation characteristics of a film forming inhibitor blend. The data show corrosion inhibition begins with the initial dose and corrosion rates continue to improve over an 8-day period.
There are difficulties encountered when treating multi-metal systems, especially when they contain aluminum components. The results presented in this paper show filming forming amines offer an effective corrosion inhibitor alternative to traditional chemistries, with possibilities for use in a variety of water systems including: hot, cold, open, or closed.
References
1. M. LaBrosse and D. Erickson. “Pilot Research to Determine Effective Aluminum Corrosion inhibition”, The Analyst, Summer 2017, 23-27
2. M. Jack 2015. “The interaction of a film-forming amine with surfaces of a recirculating experimental water loop”, heatexchangerfouling.com 2015, 112
3. 6. S. Rey and G. Reggiani, 2005. “Molybdate and Non-Molybdate Options for Closed Systems,” Association of Water Technologies
4. Pensini, E., Water Resources and Industry (2017), http://dx.doi.org/10.1016/j.wri.2017.11.001
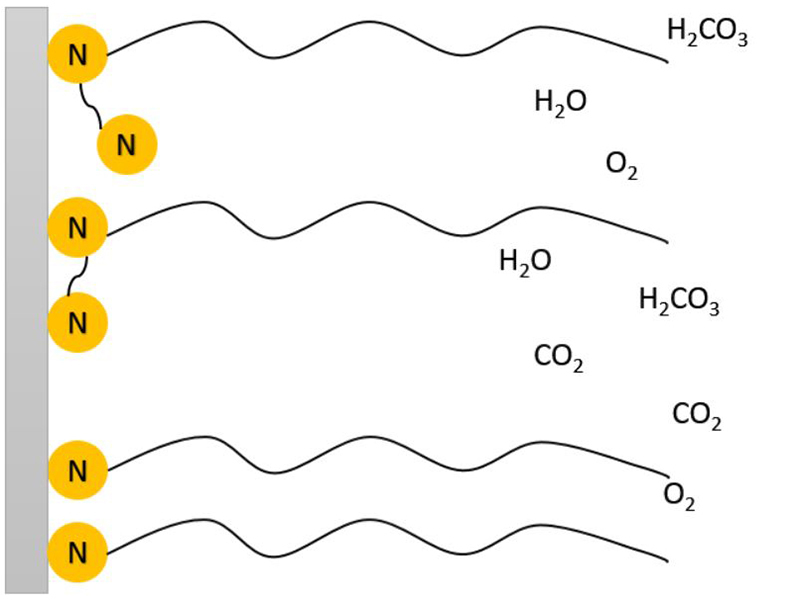

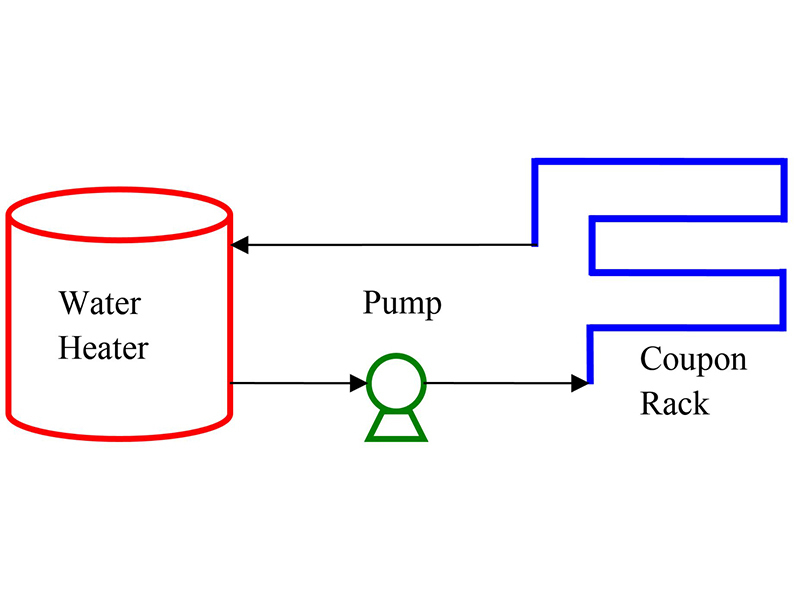
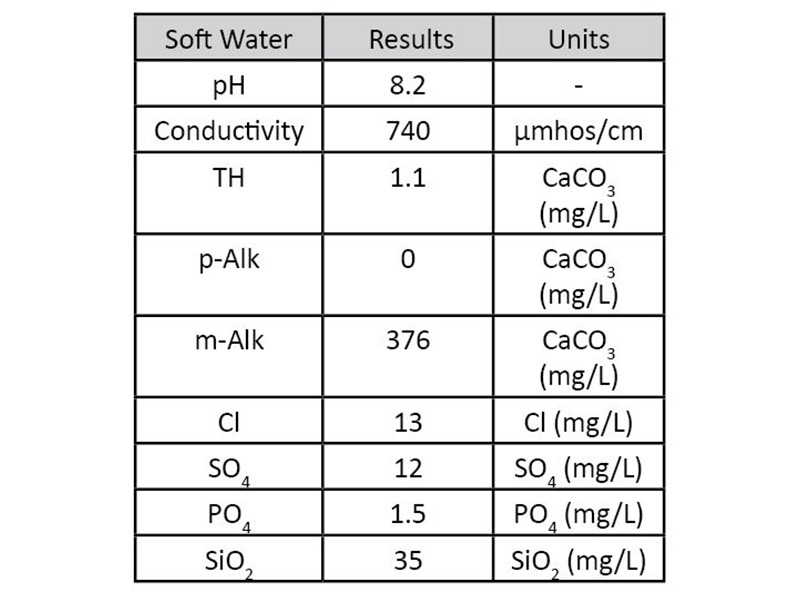
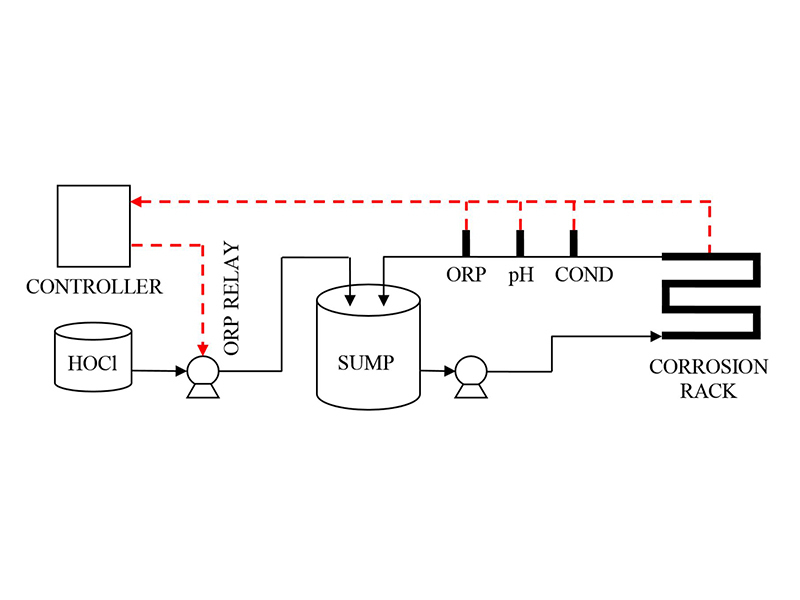
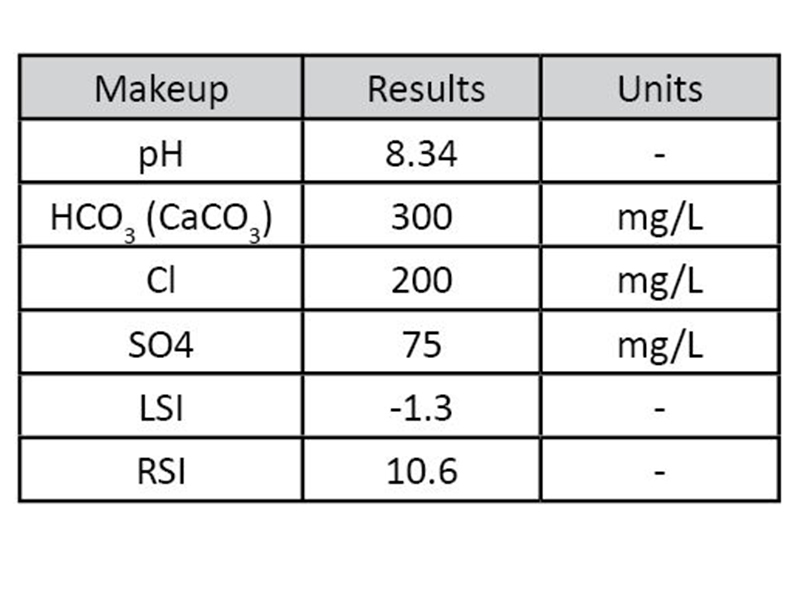
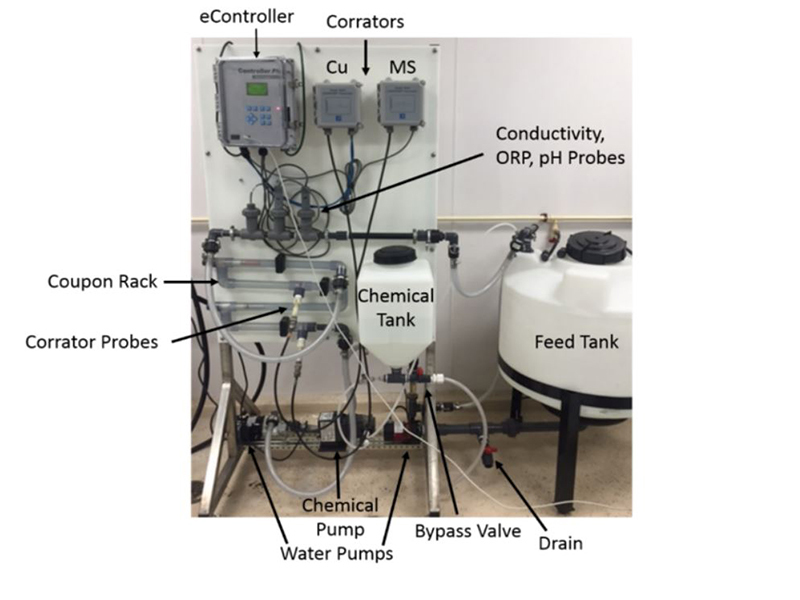
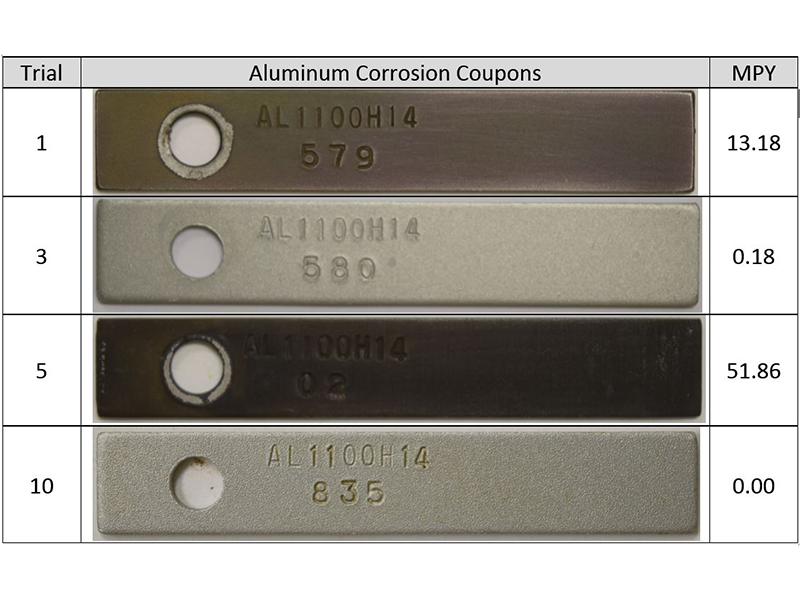
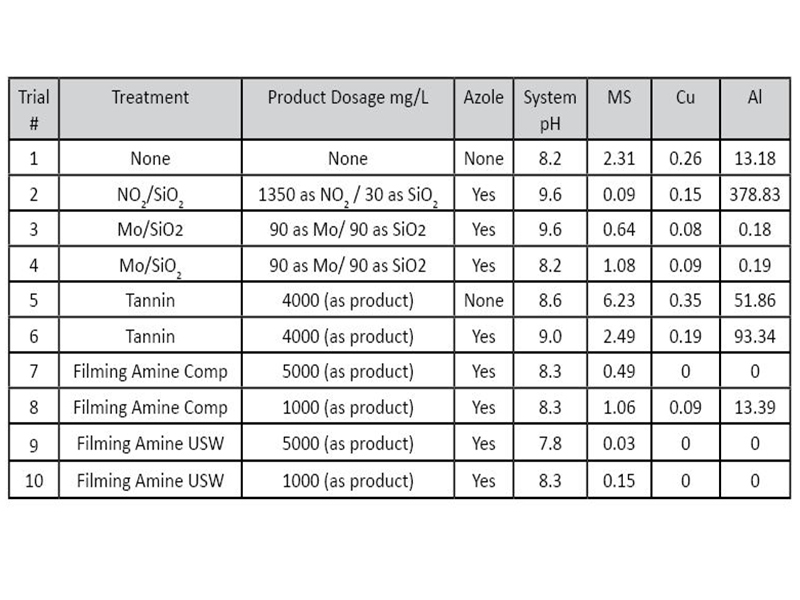
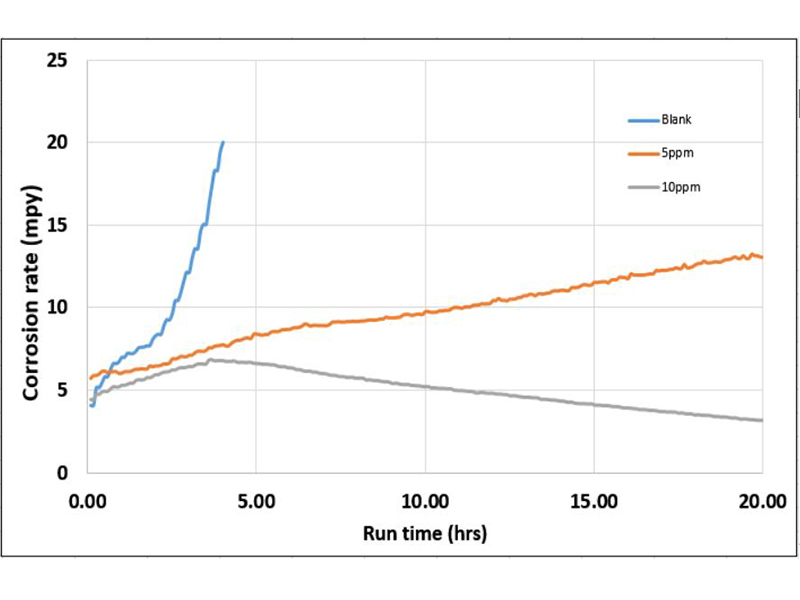
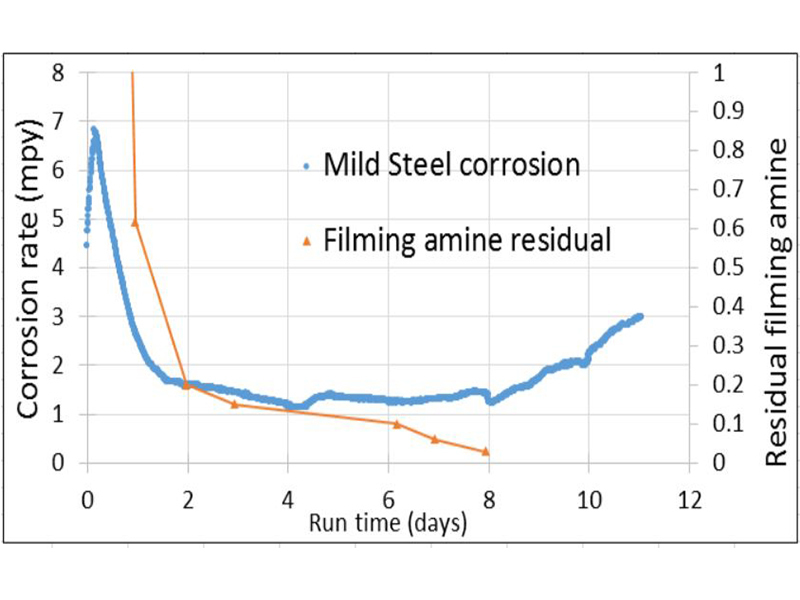