A new liquid hydrogen production facility was built to meet increasing demand from fuel cell electric vehicles (FCEVs). Hydrogen is produced using steam, which requires demineralized water to protect asset integrity and product quality. The plant needed a robust pre-treatment system to convert the municipal water supply to suitable demineralized standards.
Hydrogen is known as an “energy carrier” because the energy used to make it can be harnessed on-demand. A fuel cell converts hydrogen into electricity emission-free, forming water as the only byproduct. While battery electric vehicles (BEVs) require charging from the power grid, FCEVs are filled with hydrogen much like conventional vehicles and gasoline. Compared to BEVs, hydrogen refueling is faster than battery charging, and FCEVs achieve longer ranges of travel, especially larger vehicles like trucks and buses. Transportation generates an estimated one-fifth of global carbon dioxide (CO2) emissions, three quarters of which come from road vehicles that burn fossil fuels. Governments across the globe are promoting electric vehicles to help curb greenhouse gas emissions (GHG), increasing the importance of hydrogen.
Hydrogen is known as an “energy carrier” because the energy used to make it can be harnessed on-demand. A fuel cell converts hydrogen into electricity emission-free, forming water as the only byproduct. While battery electric vehicles (BEVs) require charging from the power grid, FCEVs are filled with hydrogen much like conventional vehicles and gasoline. Compared to BEVs, hydrogen refueling is faster than battery charging, and FCEVs achieve longer ranges of travel, especially larger vehicles like trucks and buses. Transportation generates an estimated one-fifth of global carbon dioxide (CO2) emissions, three quarters of which come from road vehicles that burn fossil fuels. Governments across the globe are promoting electric vehicles to help curb greenhouse gas emissions (GHG), increasing the importance of hydrogen.
Hydrogen gas at natural temperatures and pressures takes up a lot of space. However, gases can be compressed or cooled to reduce their volume, benefiting bulk transport and storage. New production facilities are making liquid hydrogen that can be more effectively transported to distant fueling stations using cryogenic tanker vehicles.
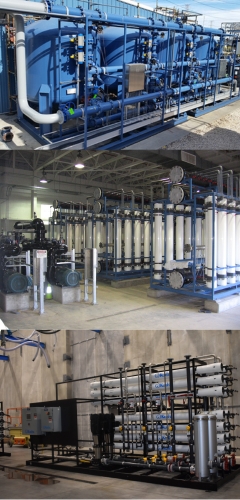
Firstly, VertaCell™ media filters remove suspended solids that may be present in the source water. These vertical pressure filters offer flexibility for redundancy and future expansion, allowing ease of both installation and maintenance.
Secondly, a U-Flex™ ultrafiltration system removes any remaining fine solids not tolerated by reverse osmosis (RO). The hollow fiber membrane technology’s small and uniform pores remove suspended particulate matter that may pass through a conventional media filter.
Thirdly, a Flux™ RO system removes dissolved solids and minerals. The two-pass RO configuration uses two membranes in series to meet the strict treatment specification. The finished water has a conductivity of less than one microsiemen per centimeter (μS/cm), meaning the dissolved solids concentration is one thousand times lower than the original water supply.
Kurita also supplied factory-tested control systems with touchscreen interfaces. This automates system functions like service modes, backwash, and cleaning to minimize downtime and reduce operating labor. Kurita offered Avista Membrane Treatment Solutions, a combination of both chemical and services, to ensure optimal performance and extend equipment life.
With the water now meeting standards, it can be converted to steam that is used to make hydrogen.
With Kurita’s pre-treatment system, the liquid hydrogen facility is empowering the use of FCEVs by bolstering the available hydrogen at local fueling stations. These projects legitimize global efforts to promote the use of FCEVs and minimize pollution from conventional transportation methods. Kurita’s integrated water treatment system plays a critical role by delivering demineralized water necessary for reliable production of liquid hydrogen while protecting their assets and product quality.
With Kurita’s pre-treatment system, the liquid hydrogen facility is empowering the use of FCEVs by bolstering the available hydrogen at local fueling stations. These projects legitimize global efforts to promote the use of FCEVs and minimize pollution from conventional transportation methods. Kurita’s integrated water treatment system plays a critical role by delivering demineralized water necessary for reliable production of liquid hydrogen while protecting their assets and product quality.